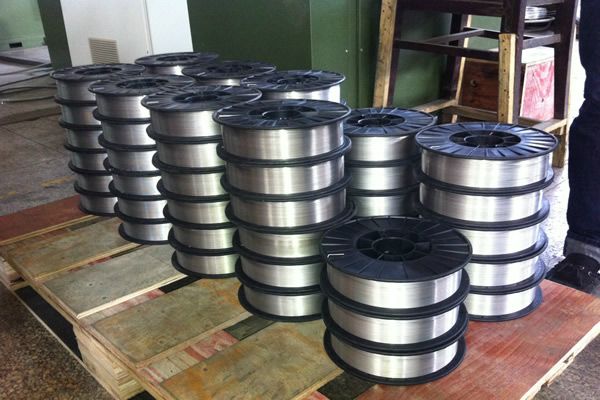
In the demanding world of high-temperature and corrosive environments, the integrity of welded joints is paramount. This is where the exceptional properties of Inconel 600 welding wire come into play. Renowned for its superior resistance to heat, corrosion, and oxidation, Inconel 600 is a critical alloy used in various industries, and its welding wire counterpart is essential for creating robust and reliable welds in challenging conditions.
Understanding Inconel 600’s Unique Properties
Inconel 600 is a nickel-chromium alloy known for its remarkable performance in extreme environments. Its high nickel content provides excellent resistance to reducing environments, while the chromium content offers resistance to oxidizing conditions. This combination makes it suitable for applications involving high temperatures, corrosive chemicals, and high-stress situations.
When it comes to welding, Inconel 600 welding wire inherits these exceptional properties, ensuring that the welded joints maintain the same level of resistance as the base material. This is crucial for applications where the weld itself is subjected to the same harsh conditions as the surrounding components.
Applications Where Inconel 600 Welding Wire Shines
The unique characteristics of Inconel 600 welding wire make it indispensable in a wide range of applications:
- Nuclear Industry: In nuclear reactors and related equipment, Inconel 600 is used for its resistance to high temperatures and corrosive coolants.
- Chemical Processing: Chemical plants utilize Inconel 600 welding wire to fabricate equipment that handles corrosive acids and alkalis.
- Aerospace: In aircraft and spacecraft components, Inconel 600 is used for its high-temperature strength and resistance to oxidation.
- Heat Treating: Furnaces and heat exchangers rely on Inconel 600 for its ability to withstand extreme temperatures.
- Power Generation: In power plants, Inconel 600 is used in boiler components and other high-temperature applications.
Key Considerations When Using Inconel 600 Welding Wire
While Inconel 600 welding wire offers exceptional performance, successful welding requires careful consideration of several factors:
- Welding Process Selection: Inconel 600 can be welded using various processes, including Gas Tungsten Arc Welding (GTAW), Gas Metal Arc Welding (GMAW), and Shielded Metal Arc Welding (SMAW). The choice of process depends on the specific application and the desired weld quality.
- Surface Preparation: Thorough cleaning of the base material is essential to remove any contaminants that could compromise the weld quality.
- Heat Input Control: Controlling the heat input during welding is crucial to prevent excessive heat-affected zones and maintain the desired microstructure.
- Filler Metal Selection: Choosing the correct filler metal is essential to ensure compatibility with the base material and achieve the desired weld properties.
- Post-Weld Heat Treatment: In some cases, post-weld heat treatment may be required to relieve residual stresses and optimize the weld’s performance.
Advantages of Inconel 600 Welding Wire
- High-Temperature Strength: Maintains its strength at elevated temperatures.
- Excellent Corrosion Resistance: Resists a wide range of corrosive environments.
- Oxidation Resistance: Prevents scaling and degradation at high temperatures.
- Weldability: Can be readily welded using various welding processes.
- Reliability: Provides robust and reliable welded joints in demanding applications.
In conclusion, Inconel 600 welding wire is a vital material for creating high-quality welds in challenging environments. Its exceptional properties make it the preferred choice for applications where high-temperature strength, corrosion resistance, and oxidation resistance are critical. By understanding the key considerations and following proper welding procedures, engineers and fabricators can harness the power of Inconel 600 to create reliable and long-lasting welded components.
Leave a Reply