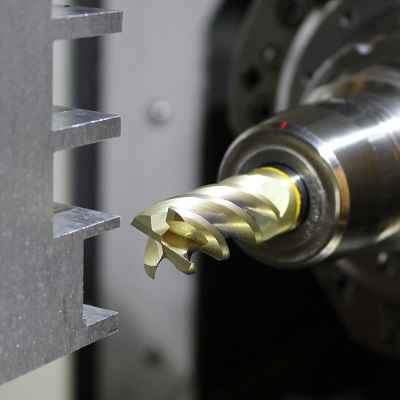
In the world of precision machining, achieving high-quality cuts and finishes is essential. However, one common issue that machinists often encounter is chatter, a phenomenon that can negatively impact both the surface finish of a part and the life of cutting tools. Chatter in machining can manifest as undesirable vibrations, leading to irregularities in the workpiece and inefficient operations. In this article, we will explore what chatter in machining is, its causes, effects, and how to prevent or mitigate it to improve the quality and efficiency of machining operations.
What is Chatter in Machining?
Chatter in machining refers to the vibrations that occur between the cutting tool and the workpiece during the cutting process. These vibrations, which can vary in frequency and amplitude, result from an interaction between the machine tool, cutting tool, and the material being machined. The effect of chatter is often visible as a rough surface finish, increased tool wear, and even damage to the machine components in severe cases.
Chatter can occur in any type of machining operation, whether itβs milling, turning, drilling, or grinding. Itβs a dynamic process that typically happens when there is an imbalance or instability in the cutting conditions. This can cause the tool to lose contact with the workpiece momentarily, followed by a sudden re-engagement, which leads to a repetitive pattern of impact. These vibrations are not only a quality issue but can also compromise the structural integrity of both the workpiece and the machine.
Causes of Chatter in Machining
Chatter is a complex phenomenon, and there are several factors that can contribute to its occurrence. Below are the primary causes of chatter in machining:
1. Resonance and Natural Frequencies
Every machine tool and cutting tool has a natural frequency of vibration, which is determined by factors such as its structure, material, and geometry. If the cutting conditions cause the frequency of the toolβs vibration to match or come close to its natural frequency, resonance occurs. This results in amplified vibrations that lead to excessive chatter. In other words, the vibrations from the cutting process are reinforced by the tool’s own frequency, exacerbating the problem.
2. Cutting Forces
The forces generated during cutting, such as radial, axial, and tangential forces, can cause the tool to deflect and oscillate. When these forces become excessive or are not distributed evenly, they can induce vibrations in the tool and the workpiece, leading to chatter. For example, if the cutting force exceeds the stiffness of the machine or the tool, it can result in significant vibrations.
3. Tool Wear
As tools wear over time, their cutting edges can become irregular or damaged. This can create an imbalance in the cutting process, where the tool may no longer cut smoothly. The irregularity in the cutting edge can lead to periodic engagement and disengagement with the workpiece, which promotes vibrations and chatter. Tool wear is particularly problematic in high-precision applications, where even slight imperfections can lead to quality issues.
4. Improper Machine Setup
The setup of the machining operation is critical for preventing chatter. Factors such as tool overhang, incorrect clamping of the workpiece, and poor alignment can all contribute to an unstable cutting environment. A long tool overhang, for instance, can lead to a lack of rigidity, making the tool more susceptible to vibrations. Similarly, improperly mounted workpieces can cause uneven cutting forces, leading to chatter.
5. High Cutting Speeds
While increasing cutting speed can enhance productivity, it also raises the risk of chatter. High cutting speeds increase the frequency and intensity of the forces acting on the tool and workpiece, which can lead to the tool vibrating and bouncing off the surface. If the cutting speed exceeds the optimal value for a particular material or operation, it can make the machine more susceptible to chatter.
6. Tool Geometry and Material
The design and material of the cutting tool also play a role in chatter formation. A tool with poor geometry or insufficient clearance angles can experience more resistance during cutting, creating additional forces that can lead to chatter. Similarly, hard materials that are difficult to machine can exacerbate the problem by generating higher cutting forces and inducing vibrations in the tool.
7. Poor Surface Finish
In some cases, the workpiece material itself may have an inconsistent surface or hardness. This unevenness can cause the tool to engage and disengage irregularly, leading to vibrations. A material with a non-uniform structure or inconsistent hardness can cause the tool to cut unevenly, which contributes to chatter.
Effects of Chatter in Machining
The occurrence of chatter can have several negative effects on the machining process, the quality of the workpiece, and the longevity of tools and machines. The primary effects of chatter include:
1. Poor Surface Finish
Chatter results in a rough, uneven surface finish on the workpiece. The vibrations cause the cutting tool to intermittently lose contact with the surface, creating patterns of peaks and valleys that are visible on the final part. A poor surface finish not only affects the aesthetic quality of the part but can also impact its functionality, particularly in precision applications where smooth surfaces are critical.
2. Increased Tool Wear
When chatter occurs, the tool experiences higher levels of stress and wear due to the irregular engagement with the workpiece. These vibrations lead to higher rates of tool wear, particularly at the cutting edges. In severe cases, the tool can become damaged or chipped, necessitating more frequent tool changes, increasing downtime, and raising overall machining costs.
3. Reduced Machining Efficiency
Chatter can significantly reduce the efficiency of a machining operation. It leads to the need for slower cutting speeds and more frequent passes to achieve the desired finish. This not only increases machining time but also reduces productivity, which is counterproductive to the goals of many machining operations.
4. Damage to the Machine Tool
In some cases, prolonged chatter can damage the machine tool itself. The continuous vibrations can lead to issues with the machine’s bearings, spindle, and other critical components. This damage can cause increased maintenance costs, downtime, and in extreme cases, the need for equipment replacement.
5. Dimensional Inaccuracies
Chatter can result in dimensional inaccuracies in the workpiece. If the tool is vibrating excessively during the cutting process, it may not maintain the correct cutting path, leading to variations in the partβs dimensions. This is particularly problematic in high-precision applications, where tolerances must be strict.
How to Prevent and Mitigate Chatter in Machining
While chatter is a common issue in machining, there are several strategies and techniques that can be employed to minimize or eliminate its occurrence.
1. Optimize Cutting Parameters
One of the most effective ways to reduce chatter is to optimize the cutting parameters, such as cutting speed, feed rate, and depth of cut. Slower cutting speeds and lower feed rates often result in reduced cutting forces and vibration. Using optimal cutting parameters for the specific material and machining operation can reduce the likelihood of chatter.
2. Use Rigidity and Stability
Ensure that the machine, tool, and workpiece are set up with maximum rigidity. Shortening the tool overhang and using a stiffer tool holder can help reduce tool deflection and vibration. Additionally, ensure that the workpiece is securely clamped to avoid any movement during cutting.
3. Tool Selection
Using a tool with the appropriate geometry and material for the job can help reduce chatter. Tools with optimized cutting edges and coatings can cut more smoothly, reducing resistance and minimizing vibrations. Regular inspection and maintenance of tools are also essential to avoid worn or damaged cutting edges, which can exacerbate chatter.
4. Damping Systems
Some modern machining centers are equipped with damping systems or vibration absorption technologies that reduce the impact of chatter. These systems are designed to absorb vibrations and prevent them from traveling through the machine, thereby stabilizing the cutting process.
5. Proper Machine Setup
Ensure that the machine is properly aligned and calibrated before starting the machining operation. A well-aligned machine will operate more smoothly, reducing the risk of chatter. Additionally, ensuring the cutting tool is aligned correctly with the workpiece can help maintain stable cutting forces.
6. Reduce Cutting Depth
Reducing the depth of cut can help reduce the forces acting on the tool and prevent excessive vibration. If chatter occurs, reducing the cutting depth for subsequent passes can improve stability and help eliminate the issue.
7. Increase Cutting Tool Stiffness
Using stiffer cutting tools and holders can prevent the tool from bending or deflecting during cutting, thereby reducing the risk of vibration. High-quality, rigid tool holders are designed to absorb vibrations and provide a more stable cutting environment.
8. Vibration Monitoring
Using vibration monitoring equipment can help detect chatter early. Monitoring vibrations during machining can provide valuable feedback, allowing machinists to make real-time adjustments to cutting parameters and setup to mitigate chatter before it becomes a major issue.
Conclusion
Chatter is a common problem in machining that can negatively impact part quality, tool life, and machine performance. Understanding its causes and effects is crucial for taking the necessary steps to minimize or eliminate chatter during machining operations. By optimizing cutting parameters, using proper tooling, improving machine setup, and incorporating damping technologies, machinists can significantly reduce the occurrence of chatter. In turn, this leads to improved surface finishes, enhanced productivity, and a more efficient and cost-effective machining process.
Leave a Reply