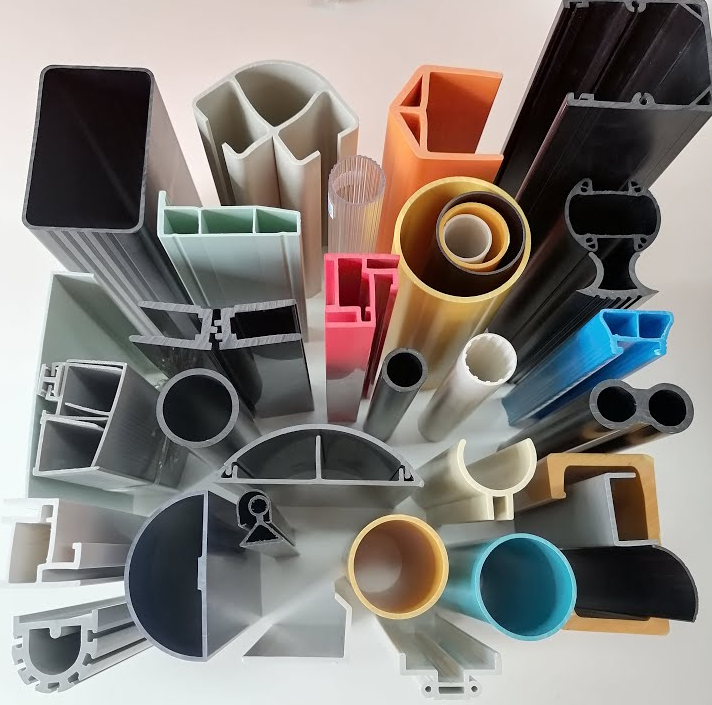
In today’s fast-paced manufacturing world, custom plastics and injection molding have become indispensable for creating high-quality, durable, and cost-effective products. From automotive parts to medical devices, consumer electronics to household goods, custom plastics and injection molding play a critical role in shaping the products we use every day.
If you’re looking to understand the ins and outs of custom plastics and injection molding, you’ve come to the right place. This comprehensive guide will walk you through everything you need to know about these processes, their benefits, applications, and how to choose the right partner for your project.
What Are Custom Plastics?
Custom plastics refer to plastic materials that are specifically designed and manufactured to meet unique requirements. Unlike off-the-shelf plastic products, custom plastics are tailored to fit precise specifications, including size, shape, color, strength, and functionality.
Why Choose Custom Plastics?
- Tailored Solutions: Custom plastics are designed to meet exact needs, ensuring optimal performance for your application.
- Cost-Effectiveness: By producing plastics tailored to your requirements, you can reduce waste and save on material costs.
- Durability and Strength: Custom plastics can be engineered to withstand specific environmental conditions, such as extreme temperatures or chemical exposure.
- Aesthetic Appeal: Custom plastics allow for unique designs, colors, and finishes that align with your brand or product vision.
What Is Injection Molding?
Injection molding is a manufacturing process used to produce plastic parts in large volumes. It involves injecting molten plastic material into a mold, where it cools and solidifies into the desired shape. This process is highly efficient, repeatable, and capable of producing complex geometries with tight tolerances.
How Does Injection Molding Work?
- Material Selection: The process begins with selecting the right plastic material based on the product’s requirements.
- Melting: The plastic pellets are melted in a heated barrel.
- Injection: The molten plastic is injected into a custom-designed mold under high pressure.
- Cooling: The plastic cools and solidifies inside the mold.
- Ejection: The finished part is ejected from the mold, ready for use or further processing.
Advantages of Injection Molding
- High Efficiency: Injection molding can produce thousands of parts in a short time, making it ideal for mass production.
- Precision and Consistency: The process ensures high accuracy and uniformity across all parts.
- Versatility: Injection molding can be used with a wide range of plastic materials, including thermoplastics, elastomers, and composites.
- Low Labor Costs: Once the mold is created, the process is largely automated, reducing labor expenses.
Applications of Custom Plastics and Injection Molding
Custom plastics and injection molding are used across a wide range of industries. Here are some of the most common applications:
- Automotive Industry
- Interior and exterior components (dashboards, bumpers, door panels)
- Engine parts (covers, housings, connectors)
- Lightweight components to improve fuel efficiency
- Medical and Healthcare
- Surgical instruments
- Implants and prosthetics
- Medical device housings and components
- Consumer Electronics
- Smartphone cases
- Laptop and tablet components
- Connectors and cables
- Packaging
- Bottles, caps, and containers
- Custom packaging solutions
- Tamper-evident seals
- Aerospace
- Lightweight components for aircraft
- Durable parts for extreme conditions
- Custom fittings and connectors
- Household Goods
- Kitchen utensils
- Storage containers
- Furniture components
Benefits of Combining Custom Plastics with Injection Molding
When custom plastics are paired with injection molding, the result is a highly efficient and cost-effective manufacturing process. Here’s why this combination is so powerful:
- Customization at Scale: Injection molding allows for the mass production of custom plastic parts, ensuring consistency and quality across large volumes.
- Reduced Waste: The precision of injection molding minimizes material waste, making it an eco-friendly option.
- Faster Turnaround Times: With advanced machinery and automation, injection molding can produce parts quickly, reducing lead times.
- Cost Savings: The ability to produce large quantities of custom parts at a low per-unit cost makes injection molding a cost-effective solution.
Choosing the Right Material for Custom Plastics and Injection Molding
Selecting the right plastic material is crucial for the success of your project. Here are some of the most commonly used materials in custom plastics and injection molding:
- Polypropylene (PP)
- Lightweight and durable
- Resistant to chemicals and moisture
- Ideal for packaging, automotive parts, and household goods
- Acrylonitrile Butadiene Styrene (ABS)
- Strong and impact-resistant
- Easy to mold and finish
- Commonly used in consumer electronics and automotive components
- Polycarbonate (PC)
- High strength and transparency
- Resistant to heat and impact
- Suitable for medical devices, eyewear, and electronic components
- Polyethylene (PE)
- Lightweight and flexible
- Excellent chemical resistance
- Used in packaging, bottles, and containers
- Nylon (Polyamide)
- High strength and wear resistance
- Ideal for gears, bearings, and industrial components
- Thermoplastic Elastomers (TPE)
- Flexible and durable
- Combines the properties of rubber and plastic
- Used in seals, gaskets, and soft-touch components
How to Choose the Right Partner for Custom Plastics and Injection Molding
Selecting the right manufacturer is critical to the success of your project. Here are some factors to consider when choosing a partner for custom plastics and injection molding:
- Experience and Expertise
- Look for a manufacturer with a proven track record in your industry.
- Ensure they have experience working with the materials and processes you need.
- Quality Assurance
- Choose a partner with robust quality control processes in place.
- Certifications like ISO 9001 are a good indicator of quality standards.
- Customization Capabilities
- Ensure the manufacturer can accommodate your specific design and material requirements.
- Look for advanced capabilities like 3D printing for prototyping.
- Production Capacity
- Assess the manufacturer’s ability to handle your production volume.
- Ensure they have the necessary equipment and resources to meet your deadlines.
- Cost-Effectiveness
- Request detailed quotes and compare pricing.
- Consider the total cost, including tooling, materials, and labor.
- Customer Support
- Choose a partner who offers excellent communication and support throughout the project.
- Look for a manufacturer who is responsive and willing to collaborate.
The Future of Custom Plastics and Injection Molding
As technology continues to advance, the future of custom plastics and injection molding looks brighter than ever. Here are some trends to watch:
- Sustainable Materials
- The demand for eco-friendly plastics, such as biodegradable and recycled materials, is on the rise.
- Manufacturers are adopting greener practices to reduce their environmental impact.
- Advanced Technologies
- Innovations like 3D printing and AI-driven design are revolutionizing the industry.
- Smart manufacturing techniques are improving efficiency and precision.
- Miniaturization
- The trend toward smaller, more complex components is driving advancements in micro-injection molding.
- Customization
- As consumer demand for personalized products grows, the ability to produce highly customized plastics will become increasingly important.
Conclusion
Custom plastics and injection molding are at the heart of modern manufacturing, offering unparalleled flexibility, efficiency, and cost-effectiveness. Whether you’re developing a new product or optimizing an existing one, understanding these processes can help you make informed decisions and achieve the best possible results.
By partnering with an experienced and reliable manufacturer, you can unlock the full potential of custom plastics and injection molding for your project. From material selection to design and production, the right partner will guide you every step of the way, ensuring a seamless and successful outcome.
If you’re ready to take your product to the next level, contact a trusted custom plastics and injection molding provider today. With their expertise and your vision, the possibilities are endless.
Leave a Reply