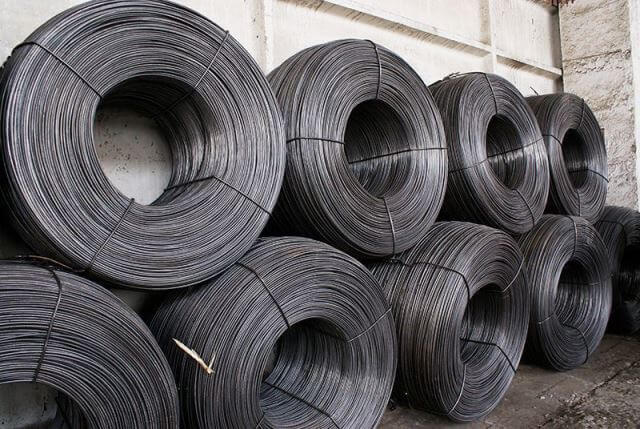
Inconel 600 welding wire is critical in industries where reliability and performance are paramount. Known for its exceptional strength and corrosion resistance, this welding wire significantly ensures durable and long-lasting welds. But what makes Inconel 600 welding wire so effective? Let’s explore the science behind its strength and why it’s the preferred choice for demanding welding applications.
What is Inconel 600?
Inconel 600 is a nickel-chromium-iron alloy designed to perform in extreme environments. Its composition provides an excellent balance of mechanical strength, corrosion resistance, and thermal stability. These characteristics make it suitable for applications involving high temperatures, corrosive chemicals, and stress.
The primary components of Inconel 600 are:
- Nickel (72% minimum): Provides corrosion resistance and enhances durability.
- Chromium (14-17%): Offers oxidation resistance and adds to the material’s strength.
- Iron (6-10%): Improves structural integrity.
These elements work together to create a welding wire that is both versatile and robust.
Key Features of Inconel 600 Welding Wire
- High-Temperature Resistance
One of the standout features of Inconel 600 welding wire is its ability to withstand extreme temperatures. This makes it ideal for applications in furnaces, heat exchangers, and nuclear reactors. Even at temperatures exceeding 1000°C, Inconel 600 maintains its mechanical integrity and resists deformation.
- Corrosion Resistance
Inconel 600 welding wire excels in environments that would quickly degrade other materials. It resists oxidation, pitting, and stress-corrosion cracking in both acidic and alkaline conditions. This property is particularly useful in industries like chemical processing and marine engineering, where exposure to harsh chemicals is common.
- Versatility
Inconel 600 welding wire can be used to join a wide range of materials, including dissimilar metals. Its compatibility with various base metals makes it a go-to option for complex welding tasks.
- Strength and Ductility
The alloy’s unique composition ensures high tensile strength and ductility. This combination allows the welding wire to create joints that are both strong and flexible, minimizing the risk of cracking under stress.
Applications of Inconel 600 Welding Wire
The properties of Inconel 600 welding wire make it indispensable in several industries:
- Aerospace
In aerospace engineering, materials are exposed to extreme heat and pressure. Inconel 600 welding wire is used to join components in jet engines, exhaust systems, and other high-performance parts. Its resistance to thermal fatigue ensures the reliability of these critical systems.
- Chemical Processing
Chemical plants rely on Inconel 600 welding wire to join pipes, reactors, and heat exchangers. The wire’s ability to withstand aggressive chemicals and high temperatures makes it essential for maintaining the integrity of these systems.
- Marine Engineering
Marine environments are notorious for their corrosive effects on materials. Inconel 600 welding wire is often used in shipbuilding and offshore platforms to create welds that resist saltwater corrosion and mechanical stress.
- Nuclear Industry
Inconel 600 welding wire is a preferred choice in nuclear reactors due to its ability to withstand radiation, high temperatures, and corrosive conditions. It is commonly used in steam generators and fuel rod components.
- Power Generation
Power plants require materials that can handle high-pressure steam and corrosive gases. Inconel 600 welding wire ensures durable welds in turbines, boilers, and heat exchangers, contributing to efficient and reliable energy production.
Why Inconel 600 Welding Wire Outperforms Other Options
Compared to conventional welding wires made from stainless steel or carbon steel, Inconel 600 offers several advantages:
- Superior Corrosion Resistance
While stainless steel provides decent corrosion resistance, it falls short in highly acidic or alkaline environments. Inconel 600’s unique composition ensures superior performance in these conditions.
- Higher Temperature Tolerance
Inconel 600 welding wire can operate in temperature ranges that would weaken or degrade other materials. Its ability to maintain strength and stability under extreme heat is unmatched.
- Longevity
The durability of Inconel 600 welding wire reduces the need for frequent repairs or replacements, saving both time and costs in the long run.
- Reliability in Stressful Conditions
Whether it’s thermal cycling, mechanical stress, or exposure to corrosive agents, Inconel 600 welding wire delivers consistent performance. This reliability is critical in applications where failure is not an option.
Selecting the Right Inconel 600 Welding Wire
Choosing the right welding wire involves understanding the specific requirements of your project. Factors to consider include the operating environment, base materials, and mechanical demands. Collaborating with reputable suppliers ensures that you receive high-quality Inconel 600 welding wire that meets industry standards.
Inconel 600 welding wire is available in various diameters and specifications to suit different welding techniques, including TIG, MIG, and submerged arc welding. Its versatility and performance make it a valuable asset in achieving high-quality, durable welds.
Leave a Reply