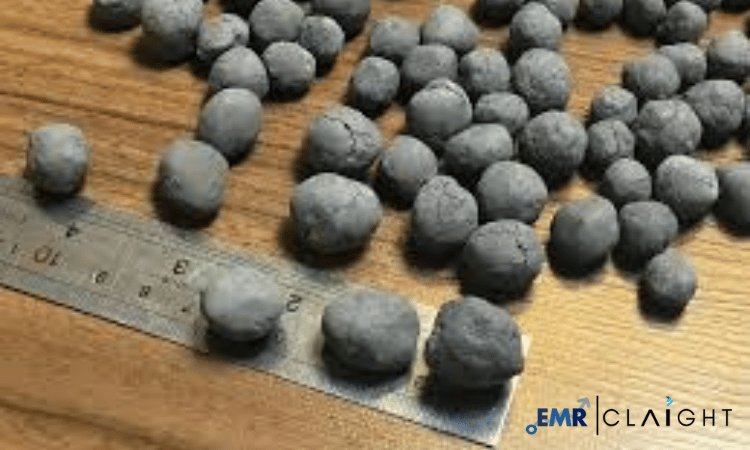
Sponge iron, also known as direct reduced iron (DRI), is a crucial raw material used in the production of steel. It is manufactured by reducing iron ore into a porous form without melting it, resulting in a material that retains its original shape and high iron content. Sponge iron is an essential component for steelmaking industries due to its energy efficiency and cost-effectiveness. With the increasing demand for steel across various sectors, setting up a sponge iron manufacturing plant presents a lucrative opportunity to cater to the growing market. This article explores the key aspects of establishing such a facility, covering production processes, machinery, and critical success factors.
Overview of Sponge Iron
Sponge iron is produced by removing oxygen from iron ore using a reducing agent, such as coal or natural gas. The process does not involve melting the iron ore, which makes it distinct from traditional methods of ironmaking. The resulting product is used as a feedstock for electric arc furnaces (EAFs) or induction furnaces in steelmaking. Sponge iron is known for its high iron content, low impurities, and uniform composition, making it a preferred choice for steel manufacturers.
Get a Free Sample Report with Table of Contents@ https://www.expertmarketresearch.com/prefeasibility-reports/sponge-iron-manufacturing-plant-project-report/requestsample
Key Components of a Sponge Iron Manufacturing Plant
-
Raw Material Procurement
The primary raw materials required are iron ore, non-coking coal, and dolomite. Ensuring a steady supply of high-quality raw materials is essential for maintaining the efficiency and quality of the manufacturing process. -
Machinery and Equipment
Efficient machinery is critical for the production of sponge iron. Key equipment includes:- Rotary Kilns: For the reduction of iron ore into sponge iron.
- Coolers: To cool the sponge iron and make it suitable for handling and storage.
- Crushers and Screens: For sizing and separation of raw materials.
- Conveyors: For material handling throughout the production process.
- Waste Heat Recovery Systems: To capture and utilise the heat generated during production.
-
Plant Layout and Design
A well-designed plant layout ensures efficient workflow, with dedicated areas for raw material handling, production, cooling, and storage. Proper ventilation and dust control measures are critical to maintaining a safe and clean working environment. -
Utilities and Infrastructure
Reliable access to electricity, water, and waste management systems is crucial for plant operations. Advanced pollution control equipment is also necessary to comply with environmental regulations. -
Workforce and Training
Skilled personnel are required to operate machinery, oversee production, and conduct quality checks. Regular training ensures workers are proficient in safety protocols and operational best practices.
Manufacturing Process of Sponge Iron
The production of sponge iron involves several stages to ensure a high-quality end product:
-
Raw Material Preparation
Iron ore, coal, and dolomite are crushed and screened to achieve the desired size and quality for the reduction process. -
Feeding and Charging
The prepared raw materials are fed into a rotary kiln, where they are subjected to high temperatures. -
Reduction Reaction
In the kiln, the iron ore reacts with the reducing agent (coal or natural gas) to remove oxygen, producing sponge iron. The kilnโs rotating motion ensures uniform heat distribution and efficient reduction. -
Cooling
The hot sponge iron is passed through a cooler to lower its temperature, making it safe for handling and storage. -
Screening and Sorting
The cooled sponge iron is screened to separate it from impurities and oversized or undersized materials. -
Packaging and Storage
The final product is packed in bulk or stored in silos for transportation to steelmaking facilities.
Applications of Sponge Iron
Sponge iron is widely used across various industries due to its high quality and versatility:
- Steel Production: Used as a primary feedstock in electric arc furnaces and induction furnaces.
- Construction: Sponge iron-based steel is used in construction projects for its strength and durability.
- Manufacturing: Employed in the production of automotive parts, machinery, and tools.
- Infrastructure Development: Used in building bridges, railways, and other critical infrastructure.
Market Potential and Demand Drivers
The growing demand for sponge iron is influenced by several factors:
-
Rising Steel Demand
The increasing use of steel in construction, automotive, and industrial applications drives the demand for sponge iron. -
Energy Efficiency
Sponge iron production consumes less energy compared to traditional ironmaking methods, making it a cost-effective option for steel manufacturers. -
Environmental Benefits
The lower carbon emissions associated with sponge iron production align with global efforts to reduce industrial pollution. -
Infrastructure Growth
Rapid urbanisation and infrastructure development projects in emerging economies boost the demand for steel and its raw materials.
Challenges in Sponge Iron Manufacturing
-
Raw Material Availability
Fluctuations in the supply and price of iron ore and coal can impact production costs and efficiency. -
Energy Consumption
Sponge iron production requires a significant amount of energy. Investing in energy-efficient technologies can mitigate this challenge. -
Environmental Compliance
Adhering to stringent environmental regulations requires advanced pollution control measures and waste management systems. -
Competition
The sponge iron market is competitive, with numerous players offering similar products. Differentiating through quality, efficiency, and customer service is essential.
Sustainability in Sponge Iron Manufacturing
Sustainability practices are becoming increasingly important in the sponge iron industry. Key initiatives include:
- Waste Heat Recovery: Capturing and utilising heat generated during production reduces energy consumption and lowers costs.
- Pollution Control: Installing advanced air and water pollution control systems ensures compliance with environmental standards.
- Renewable Energy Integration: Incorporating solar or wind power in plant operations reduces dependence on non-renewable energy sources.
- Recycling and Reuse: Repurposing by-products such as char or slag for other industrial applications minimises waste.
Key Success Factors for a Sponge Iron Manufacturing Plant
- Quality Assurance: Maintaining consistent quality in raw materials and finished products builds trust and long-term customer relationships.
- Operational Efficiency: Streamlining processes and investing in advanced machinery enhances productivity and reduces costs.
- Market Insights: Understanding market trends and customer needs helps manufacturers tailor their offerings to meet specific requirements.
- Sustainability Practices: Adopting eco-friendly measures strengthens the brandโs reputation and aligns with industry trends.
- Skilled Workforce: A well-trained workforce ensures smooth operations and adherence to safety standards.
By focusing on these aspects, a sponge iron manufacturing plant can cater to the growing market demand while maintaining operational efficiency and environmental responsibility.
Leave a Reply