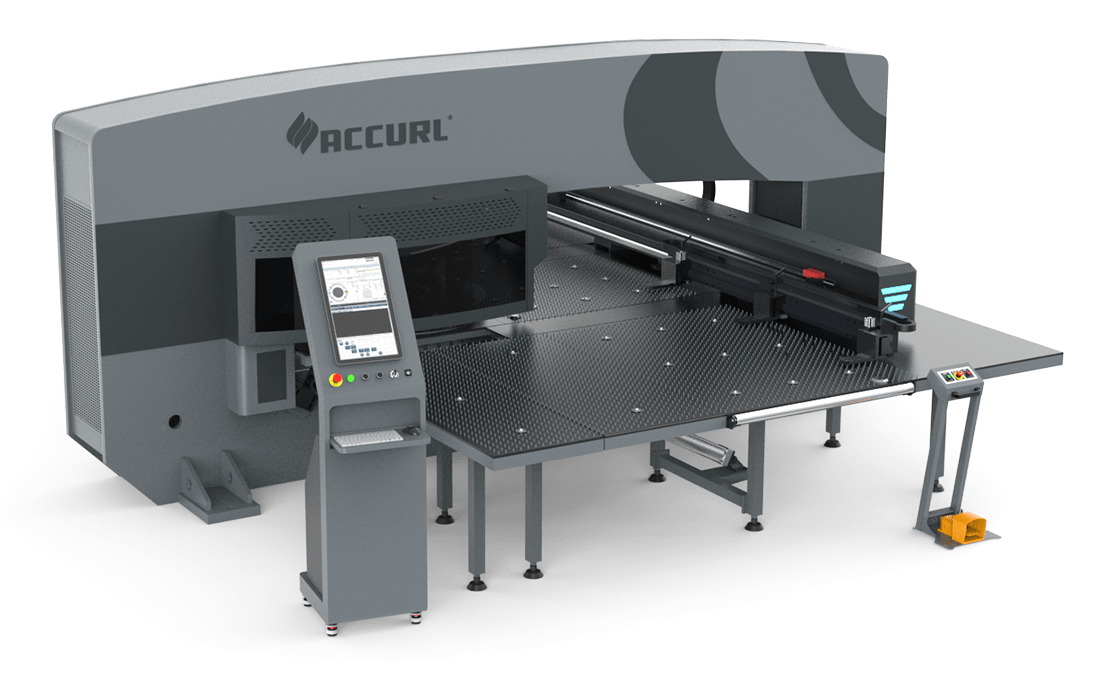
Punch presses are essential tools in the metal fabrication industry, prized for their ability to shape and cut sheet metal with precision. However, like any machinery, they are susceptible to wear and tear, leading to operational challenges. In this blog, we’ll explore common punch press problems and offer practical solutions, ensuring optimal performance and longevity for your equipment.
1. Misaligned Punch and Die
Issue: Misalignment between the punch and die can result in poor-quality cuts or uneven shapes. This issue often arises due to wear on the guide bushings or incorrect setup.
Fix:
- Regularly inspect and replace worn guide bushings.
- Use a laser alignment tool to ensure precise setup.
- Perform routine maintenance to check for signs of wear on the tooling components.
Β
2. Material Jamming or Sticking
Issue: Sheet metal jamming during operation can cause production delays and damage to the punch press. This problem often occurs when improper material thickness or lubrication is used.
Fix:
- Verify that the material thickness matches the machineβs capabilities.
- Apply appropriate lubricants to reduce friction during the punching process.
- Check the die clearance to ensure it’s suitable for the material being processed.
Β
3. Excessive Tool Wear
Issue: Punch and die tools can wear out quickly if used excessively or incorrectly, leading to poor results and downtime.
Fix:
- Use high-quality tooling materials that match the application.
- Sharpen tools regularly using a precision grinder.
- Monitor punch and die usage to avoid exceeding recommended load limits.
Β
4. Noise and Vibration
Issue: Excessive noise or vibration during operation can indicate mechanical problems, such as loose components or imbalance in the flywheel.
Fix:
- Tighten all bolts and fasteners to eliminate looseness.
- Inspect the flywheel for signs of wear or imbalance.
- Lubricate moving parts regularly to reduce friction.
Β
5. Hydraulic System Failures (For CNC Punch Presses)
Issue: CNC punch presses rely on hydraulic systems for smooth operation. Leaks, low fluid levels, or pump failures can disrupt performance.
Fix:
- Check hydraulic fluid levels and refill if necessary.
- Inspect hoses and seals for leaks and replace them promptly.
- Regularly service the hydraulic pump to maintain optimal pressure.
Β
6. Cracked or Broken Punches
Issue: Cracked or broken punches can occur due to excessive force or improper material selection, leading to downtime and additional costs.
Fix:
- Choose punches made from high-strength alloys for durability.
- Avoid overloading the punch press with material beyond its rated capacity.
- Regularly inspect punches for early signs of fatigue or damage.
7. Electrical Malfunctions
Issue: Electrical problems, such as faulty wiring or blown fuses, can disrupt automated punch press systems.
Fix:
- Conduct periodic electrical inspections to identify potential faults.
- Replace worn-out wires and ensure proper grounding.
- Use surge protectors to safeguard the system against voltage spikes.
Β
Proactive Maintenance Tips
- Implement a Preventive Maintenance Schedule to identify issues before they escalate.
- Train operators to recognize early signs of problems and perform routine inspections.
- Keep spare parts for critical components like punches, dies, and bushings to minimize downtime.
Β
Conclusion
By understanding and addressing common punch press issues, manufacturers can significantly enhance the efficiency and reliability of their operations. Regular maintenance, proper tool handling, and addressing problems promptly are key to keeping your punch press in top shape.
Would you like additional guidance or specific advice on maintaining your CNC punch press? Let us know in the comments below!
Leave a Reply