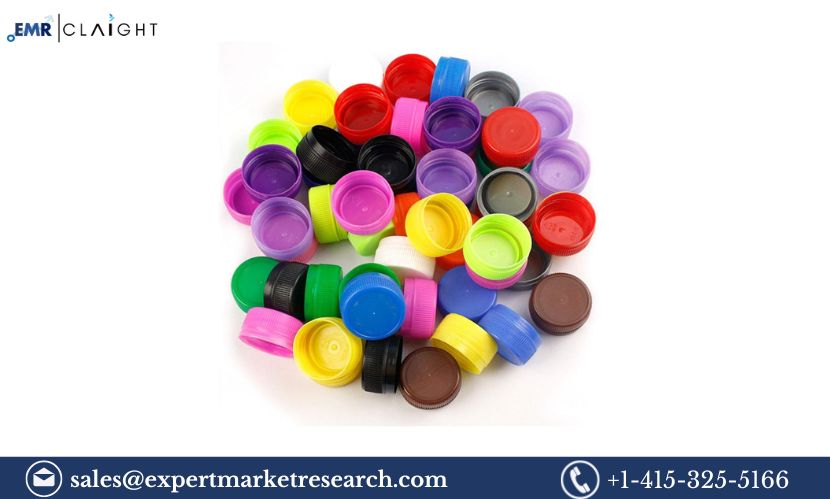
Introduction
Bottle caps are essential components of packaging for various industries, including food and beverages, pharmaceuticals, cosmetics, and household products. The demand for high-quality, durable, and tamper-evident bottle caps has surged globally, driven by the expanding packaging industry, increased focus on consumer safety, and the rising demand for convenience. The production of bottle caps involves specialized processes and technologies, making it a lucrative investment opportunity. This bottle caps manufacturing plant project report aims to provide a detailed understanding of establishing a bottle caps manufacturing plant, including production processes, equipment, market demand, cost considerations, and growth opportunities.
Key Components of Bottle Caps Manufacturing
1. Raw Materials and Supply Chain
The key raw materials used in the manufacturing of bottle caps include:
-
Plastic (Polyethylene, Polypropylene): The most commonly used materials for producing bottle caps are polyethylene (PE) and polypropylene (PP). These materials are lightweight, durable, and cost-effective.
-
Aluminum: In some applications, particularly for tamper-evident or specialty bottle caps, aluminum may be used. Aluminum caps offer high durability, and they can be designed with security features such as safety seals.
-
Additives and Colorants: These are used to enhance the properties of the caps, such as UV resistance, flexibility, and color customization.
-
Gaskets (for tamper-evident caps): A crucial component for ensuring a secure seal, gaskets are often made from rubber or other materials that can create an airtight seal when the cap is tightened.
Building a reliable supply chain for these raw materials is essential for maintaining production efficiency and ensuring product quality.
Get a Free Sample Report with Table of Contents@
2. Bottle Cap Manufacturing Process
The process of manufacturing bottle caps involves several key stages, each requiring specialized equipment and careful attention to detail. The major steps in the bottle cap production process are:
-
Injection Molding:
The most common method for manufacturing plastic bottle caps is injection molding. In this process, plastic pellets (PE or PP) are heated and injected into a mold under high pressure. The mold is designed to create the shape and size of the bottle cap, including any design features such as ridges, threads, and logos. -
Cooling and Ejection:
After injection, the plastic material is allowed to cool and solidify. Once cooled, the cap is ejected from the mold and transferred to the next stage in the production process. -
Trimming:
The bottle caps may have excess material (called flash) around the edges after molding. These areas are trimmed off using automated cutting tools to ensure that the caps have smooth edges and are properly shaped. -
Compression Molding for Gaskets:
For tamper-evident caps, a gasket is often molded separately using compression molding techniques. Rubber or other sealing materials are used to create gaskets that are then inserted into the cap. This ensures an airtight seal and increases the security and freshness of the product inside the bottle. -
Decoration (Optional):
Depending on the application and customer requirements, the caps may undergo decoration processes such as hot stamping, screen printing, or embossing. These methods can be used to add logos, brand names, or other designs on the surface of the cap. -
Inspection and Quality Control:
The bottle caps undergo thorough inspection and quality control checks to ensure they meet the required standards. Factors such as thread formation, sealing efficiency, appearance, and dimensional accuracy are tested. -
Packaging:
Once the caps are fully manufactured and tested, they are packaged into bundles or boxes and prepared for shipment. Packaging is designed to protect the caps from damage during transportation and storage.
3. Required Equipment for Manufacturing
Setting up a bottle cap manufacturing plant requires several pieces of specialized machinery and equipment, including:
-
Injection Molding Machines: These machines are used to mold plastic bottle caps by injecting melted plastic into molds.
-
Compression Molding Machines: These are used to create rubber or other sealing gaskets for tamper-evident caps.
-
Trimming Machines: These machines remove excess plastic from the edges of the bottle caps, ensuring a smooth and uniform finish.
-
Decoration Equipment: This includes machines for hot stamping, screen printing, and embossing, used to add branding or decorative designs to the caps.
-
Inspection and Testing Machines: Equipment such as vision systems, torque testers, and seal integrity testers are used to ensure the quality and functionality of the caps.
-
Packaging Machines: Automated packaging systems are used to bundle and box the finished bottle caps for shipment.
Investing in high-quality and efficient machinery is essential to meet production targets and maintain product quality.
4. Quality Control
Quality control is critical in the bottle caps manufacturing process to ensure that the final product meets industry standards and consumer expectations. Key aspects to monitor during production include:
-
Thread and Seal Integrity: The threads of the cap must be formed precisely to ensure that they fit securely on the bottle. The seal integrity is also crucial, especially for tamper-evident caps, to ensure that they provide an airtight, leak-proof seal.
-
Appearance and Finish: The cap must have a smooth surface, free of defects or blemishes. Any decoration or printing must be clear, legible, and accurately applied.
-
Dimensional Accuracy: Caps must meet specific size and shape specifications to fit the bottles they are intended for. Precision in molding and trimming is key to ensuring proper fitment.
Regular quality checks, automated inspections, and adherence to international standards such as ISO 9001 ensure consistency and product reliability.
Economic Considerations
1. Initial Investment
The initial investment for setting up a bottle cap manufacturing plant can vary depending on the scale of operations, technology, and location. The major cost components include:
-
Land and Facility: The cost of purchasing or leasing land and building the manufacturing plant.
-
Machinery and Equipment: Investment in injection molding machines, compression molding machines, trimming machines, decoration equipment, inspection systems, and packaging lines.
-
Raw Materials: The initial procurement of raw materials such as plastic resins (PE/PP), rubber for gaskets, and any required colorants or additives.
-
Labor: Hiring skilled personnel, including machine operators, quality control specialists, and administrative staff.
-
Utilities and Infrastructure: Setting up necessary utilities such as electricity, water, and waste management systems.
The total initial investment can range from several hundred thousand to millions of dollars, depending on the production capacity and level of automation.
2. Operational Costs
Operational costs for a bottle cap manufacturing plant include:
-
Raw Material Costs: The ongoing cost of procuring plastic resins, rubber for gaskets, colorants, and other additives.
-
Labor Costs: Wages for workers involved in production, quality control, maintenance, and management.
-
Energy Costs: Injection molding and compression molding processes require significant energy input, making energy costs a major operational expense.
-
Maintenance: Regular maintenance and repairs for machines and equipment to ensure continuous operation.
-
Packaging and Distribution: Costs associated with packaging the finished caps and transporting them to customers.
3. Market Demand and Pricing
The global demand for bottle caps is driven by several factors, including the growing packaging industry, increasing consumption of bottled beverages, and rising concerns over food safety and hygiene. The demand for tamper-evident and child-resistant bottle caps is also increasing, especially in the pharmaceutical and personal care sectors.
Key sectors that require bottle caps include:
-
Beverages: Soft drinks, bottled water, juices, alcoholic beverages.
-
Pharmaceuticals: Bottles for medicines, over-the-counter drugs, and supplements.
-
Food: Packaging for sauces, oils, condiments, and packaged food products.
-
Cosmetics and Household Products: Bottles for shampoos, lotions, cleaning products, and other consumer goods.
The pricing of bottle caps depends on several factors, such as material costs, production volume, and customization (e.g., printing or embossing). Standard plastic bottle caps may have a lower cost, while specialty caps (e.g., aluminum or tamper-evident) can be priced higher.
4. Regulatory Compliance
Bottle cap manufacturing plants must adhere to various regulatory standards, especially in sectors like food and pharmaceuticals, where safety and hygiene are critical. Key regulations include:
-
Food Safety Standards: Ensuring that the bottle caps used in food and beverage packaging comply with health and safety regulations (e.g., FDA regulations in the U.S.).
-
Pharmaceutical Packaging Regulations: For pharmaceutical products, the bottle caps must meet stringent requirements for tamper-evidence and child safety.
-
Environmental Regulations: Compliance with regulations regarding the use of recyclable materials, waste management, and carbon emissions from manufacturing processes.
Obtaining certifications such as ISO 9001 (quality management) and ISO 14001 (environmental management) can enhance a company’s reputation and marketability.
5. Risk MaXnagement
Some risks associated with bottle cap manufacturing include:
-
Raw Material Price Fluctuations: Variability in the prices of plastic resins and rubber can impact production costs.
-
Supply Chain Disruptions: Delays in the delivery of raw materials or machinery can cause production bottlenecks.
-
Market Competition: The bottle cap market is competitive, with many established manufacturers. New entrants must focus on innovation, quality, and customer relationships to gain a foothold.
-
Regulatory Risks: Changes in packaging regulations or new requirements for tamper-evident and child-proof caps can affect manufacturing processes.
Mitigating these risks through supply chain diversification, maintaining quality control, and staying updated with regulatory changes can help manage potential challenges.
FAQ
1. What materials are used for bottle cap manufacturing?
The most common materials are polyethylene (PE), polypropylene (PP), and aluminum. Rubber or other sealing materials are used for gaskets in tamper-evident caps.
2. How are bottle caps manufactured?
Bottle caps are manufactured using injection molding, followed by cooling, trimming, compression molding for gaskets, decoration, and quality inspection.
3. What industries use bottle caps?
Bottle caps are widely used in the beverage, pharmaceutical, food packaging, and cosmetics industries.
4. What are tamper-evident bottle caps?
Tamper-evident bottle caps are designed with security features, such as seals or bands, that show evidence if the cap has been removed or tampered with.
5. What is the cost of setting up a bottle cap manufacturing plant?
The initial investment can range from several hundred thousand to millions of dollars, depending on the scale of operations, machinery, and location.
6. How is quality control maintained in bottle cap production?
Quality control involves inspecting thread formation, seal integrity, dimensional accuracy, and surface appearance, along with regular testing to ensure product reliability.
7. What are the challenges in bottle cap manufacturing?
Challenges include raw material price fluctuations, market competition, maintaining high-quality standards, and compliance with safety and environmental regulations.
8. How can bottle cap manufacturers improve sustainability?
Using recycled materials, optimizing energy use, and reducing waste in the manufacturing process can improve sustainability and reduce environmental impact.
Media Contact
Company Name: Claight Corporation
Contact Person: Lewis Fernandas, Corporate Sales Specialist — U.S.A.
Email: sales@expertmarketresearch.com
Toll Free Number: +1–415–325–5166 | +44–702–402–5790
Address: 30 North Gould Street, Sheridan, WY 82801, USA
Website: www.expertmarketresearch.com
Aus Site: https://www.expertmarketresearch.com.au
Leave a Reply