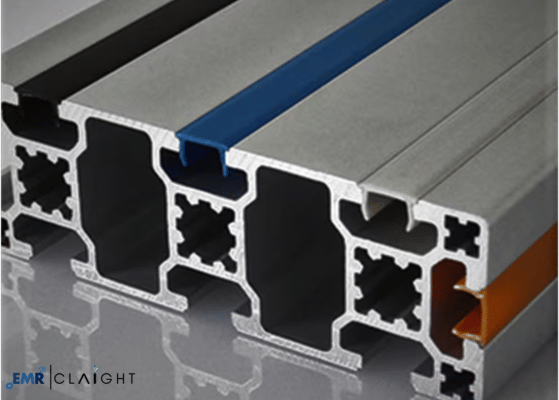
Aluminum beading is an essential product widely used in construction, automotive, and industrial applications. These versatile strips provide durability, aesthetic appeal, and functionality to various products and structures. Whether used for decorative purposes, as weatherproofing solutions, or as functional reinforcements, aluminum beadings are valued for their lightweight and corrosion-resistant properties. With the growing demand across industries, establishing an Aluminum Beading Manufacturing Plant Project presents a promising opportunity. This project requires a strategic approach, advanced manufacturing processes, and adherence to quality standards to cater to diverse market needs effectively.
Applications and Market Demand
Aluminum beading has a wide range of applications, making it a highly sought-after product in multiple industries:
- Construction: Aluminum beading is extensively used in building interiors and exteriors for aesthetic enhancements and structural reinforcements. It is commonly applied in drywall finishing, window frames, and weatherproofing.
- Automotive Industry: Beading is utilised in car door seals, window linings, and other areas requiring a lightweight, corrosion-resistant solution to ensure durability and performance.
- Industrial Applications: In manufacturing and assembly processes, aluminum beadings serve as protective barriers, decorative trims, or functional reinforcements in machinery and equipment.
The increasing focus on lightweight and durable materials across industries has significantly boosted the demand for aluminum beading, creating substantial opportunities for manufacturers.
Get a Free Sample Report with Table of Contents@ https://www.expertmarketresearch.com/prefeasibility-reports/aluminum-beading-manufacturing-plant-project-report/requestsample
Key Steps in Setting Up an Aluminum Beading Manufacturing Plant
- Market Research and Feasibility Study Conducting comprehensive market research is essential to understand the demand for aluminum beading in various industries. A feasibility study evaluates the projectβs viability by analysing production costs, market trends, and potential challenges. This ensures that the manufacturing plant aligns with market needs and customer expectations.
- Business Plan Development A detailed business plan outlines the projectβs objectives, production capacity, financial estimates, and marketing strategies. It serves as a roadmap for the plantβs establishment, ensuring efficient resource allocation and operational success. The plan also identifies potential risks and provides mitigation strategies.
- Location Selection and Infrastructure Choosing an appropriate location is critical for operational efficiency. Factors such as proximity to raw material suppliers, access to transportation networks, and availability of utilities like electricity and water should be considered. The infrastructure must include production units, storage facilities, quality control labs, and administrative offices. Compliance with zoning laws and environmental regulations is essential.
- Procurement of Equipment and Machinery Manufacturing aluminum beading requires specialised equipment, including extrusion machines, cutting tools, and finishing systems. Investing in advanced technology ensures efficient production and consistent quality. Collaborating with reliable equipment suppliers for installation and maintenance support is crucial for long-term success.
- Raw Material Sourcing The production of aluminum beading involves sourcing high-quality aluminum billets or coils. Establishing a reliable supply chain ensures a steady flow of inputs and uninterrupted production. The quality of raw materials directly affects the appearance, strength, and durability of the final product.
Manufacturing Process Overview
The production of aluminum beading involves several critical stages designed to ensure precision and quality:
- Raw Material Preparation: Aluminum billets or coils are inspected and prepared for processing.
- Extrusion: The raw material is heated and passed through extrusion dies to create beadings of the desired shape and size.
- Cutting and Shaping: The extruded aluminum is cut and shaped according to the required dimensions.
- Surface Treatment: The beadings undergo surface treatments such as anodising, powder coating, or polishing to enhance durability and aesthetic appeal.
- Quality Inspection: The finished beadings are inspected for defects and compliance with industry standards.
- Packaging and Distribution: The beadings are packaged securely and prepared for delivery to customers.
Quality Control Measures
Maintaining high-quality standards is essential in aluminum beading manufacturing. Quality control measures include:
- Raw Material Testing: Ensuring that all aluminum inputs meet the required specifications.
- Process Monitoring: Conducting regular checks during production to maintain consistency and efficiency.
- Final Product Testing: Verifying the strength, finish, and compliance of the finished beadings.
Adherence to industry certifications and regulatory standards enhances product reliability and builds customer trust.
Packaging and Distribution
Effective packaging plays a vital role in preserving the quality and appearance of aluminum beadings during storage and transportation. Packaging materials must prevent damage, scratches, or contamination. Proper labelling with detailed product information and handling instructions is essential. A robust distribution network ensures timely delivery to construction firms, automotive manufacturers, and other end-users.
Sustainability in Manufacturing
Sustainability is becoming increasingly important in aluminum manufacturing. Implementing eco-friendly practices, such as optimising energy consumption and recycling aluminum scraps, helps reduce the environmental impact of production. Using renewable energy sources and adopting advanced technologies further enhances the plantβs sustainability credentials.
Emerging Trends and Opportunities
The aluminum beading market is evolving with advancements in technology and increasing demand from various sectors. The rise of sustainable construction practices has driven the need for lightweight and eco-friendly materials like aluminum. Additionally, the growing automotive sector and innovations in decorative trims highlight the potential for market growth. Staying updated on industry trends and investing in research and development ensures competitiveness and long-term success.
Challenges in the Industry
Establishing an aluminum beading manufacturing plant involves challenges such as fluctuating raw material costs, compliance with environmental regulations, and maintaining consistent product quality. Addressing these challenges requires strategic planning, efficient resource management, and continuous innovation. Collaborating with industry experts and leveraging advanced technologies helps mitigate risks and achieve operational excellence.
Leave a Reply