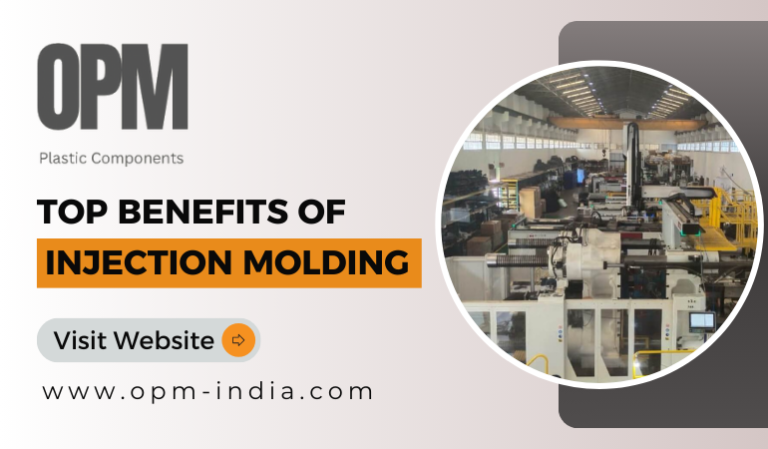
Injection molding involves circulating melting plastic into precisely formed molds before cooling and ejecting the finished product. It’s a highly repeatable method that allows businesses to manufacture large quantities of identical plastic parts with tight tolerances at a cheap cost per item.
Injection molding has several uses in a wide range of industries, including the automotive and medical industries, but it is not the best option for every project. Before deciding whether or not to injection mold your part, thoroughly examine the Benefits of injection molding and the drawbacks.
What is injection molding?
Injection molding is a method of molding that creates objects by injecting molten material into a mold. This method can be carried out with a variety of materials, including metals, glassware, elastomers, confections, and, most typically, thermoplastic and thermoset polymers.
The core of injection molding consists of its capacity to manufacture large quantities of the same item with excellent precision, making it a popular choice in mass production scenarios.
What Are the Benefits of Injection Molding?
1. High Efficiency and Fast Production
Injection molding’s efficiency and quick manufacturing times are its main advantages. This process is renowned for producing enormous quantities of products at an unmatched speed — a quality that is essential for mass production.
The injection molding process’s speed is a major factor in cutting production time and increasing output rate, which makes it a priceless tool for quickly satisfying market needs.
2. Ability to Produce Complex Geometries
Injection molding’s ability to produce intricate and complex designs is another important benefit. This procedure’s accuracy makes it possible to produce items with complex geometries that would be difficult or impossible to accomplish using alternative manufacturing techniques.
This capacity challenges the limits of what is possible in part design and geometry, opening opportunities to creativity and complexity in design.
3. Wide Range of Material Options
With a large selection of materials, injection molding is incredibly versatile. A wide variety of polymers can be used with this method, and each one gives the finished product unique qualities and appearances.
Injection molding’s wide range of material options meets a wide range of industry needs, from flexible materials for consumer items to robust polymers for automotive components.
4 . Multiple Finishes
The final appearance of the majority of injection-molded items should be smooth. It isn’t the right finish for every use, though. Injection molding enables surface finishes that don’t require secondary operations, such as etching, matte finishes, and distinctive textures, depending on the physical and chemical characteristics of the plastics employed.
5. Shorten Product Development Time
Injection molding engineers possess a variety of skills that can help OEMs develop products more quickly. This gives producers a clear competitive edge by enabling quicker production cycles and the timely release of products free of defects.
6. Reduced Waste
We at OPM take pride in our continuous environmentally beneficial green activities. However, corporate social responsibility is only one aspect of our dedication to the environment. We are aware of the financial and environmental advantages of sustainable injection molding techniques, such as the use of plastic regrind, which reduces waste and directly helps OEMs.
7 . Enhanced Design Flexibility
With the increased design flexibility that injection molding provides, designers can create intricate shapes and forms that would be difficult to achieve with other manufacturing techniques. For other applications, where design is just as critical as functionality, this creative freedom is essential.
Designers can push the limits of what is feasible in product creation by experimenting with complex shapes, internal channels, and distinctive geometries using injection molding. This adaptability not only encourages creativity but also makes it possible to develop solutions that are specifically suited to the demands of users and industry trends.
8. Integrated Features
The ability to include different features straight into the molded object is what makes injection molding unique. Hinges, fasteners, and even specific surface textures can be incorporated into a single component thanks to this method.
By integrating these characteristics into the molding process, extra assembly or adjustments are avoided, increasing manufacturing efficiency. This feature ensures a more efficient and economical production process by saving time and lowering the product’s overall complexity.
9. Reduced Assembly Costs
Since injection molding enables parts to be designed to fit together flawlessly, it drastically lowers assembly costs. This integrated method reduces the need for extra parts and procedures, like welding or fastening, which often increase assembly time and cost.
Manufacturers may speed up the assembly process and save labor costs and production delays by developing parts that easily align and connect. In sectors where speed to market is crucial, this efficiency is especially beneficial.
How OPM Helps:
Thermoplastics, thermosets, and even metals are among the many materials that can be used with injection molding. These materials can be readily combined with color pigments and other additives to modify the moldings’ appearance and functionality. Additionally, because the tooling is consistent throughout, the injection molding process provides exceptional consistency between units.
OPM is one of the top plastic injection molding manufacturers in Pune, India. Plastic injection molding is a popular manufacturing technique utilized in daily goods, despite the fact that it may seem complicated to the consumer. Because injection-molded plastic is so flexible, it may be used to create anything from complex elements to enormous items. For any plastic work, OPM will match your level of complexity. We will manufacture the product to ensure that only the best quality parts are created, whether your goal is to save time and money or satisfy the highest quality tolerances.
At OPM, we provide a variety of Injection molding Services in Pune utilizing metals or thermoplastics, ranging from low-volume prototyping at a reasonable cost to part manufacturing. Whether you require quick aluminum tooling for a quick prototype or a more robust solution for larger production runs, our team of skilled Plastic Injection Molding experts in Pune can help you find the best solution.
Conclusion
A flexible and effective manufacturing technique, injection molding has many advantages. Injection molding meets a variety of manufacturing objectives, from the ability to combine several features into a single item and guarantee consistency across production batches to the ability to mold big parts and the decreased need for finishing.
Its prominence as a pillar of contemporary production is supported by the fact that its adaptability in both design and functioning makes it a popular option across a range of industries. Injection molding is at the forefront of the industry’s ongoing evolution, evolving and adapting to satisfy the constantly shifting needs of the worldwide market.
Its scalability, automation capabilities, and material selection flexibility all contribute to its attractiveness. Injection molding keeps modern manufacturing innovative and efficient, whether it is used for small components or large-scale production. For more information on how injection molding can benefit your business, contact OPM today at sales@opm-uk.com.
Leave a Reply