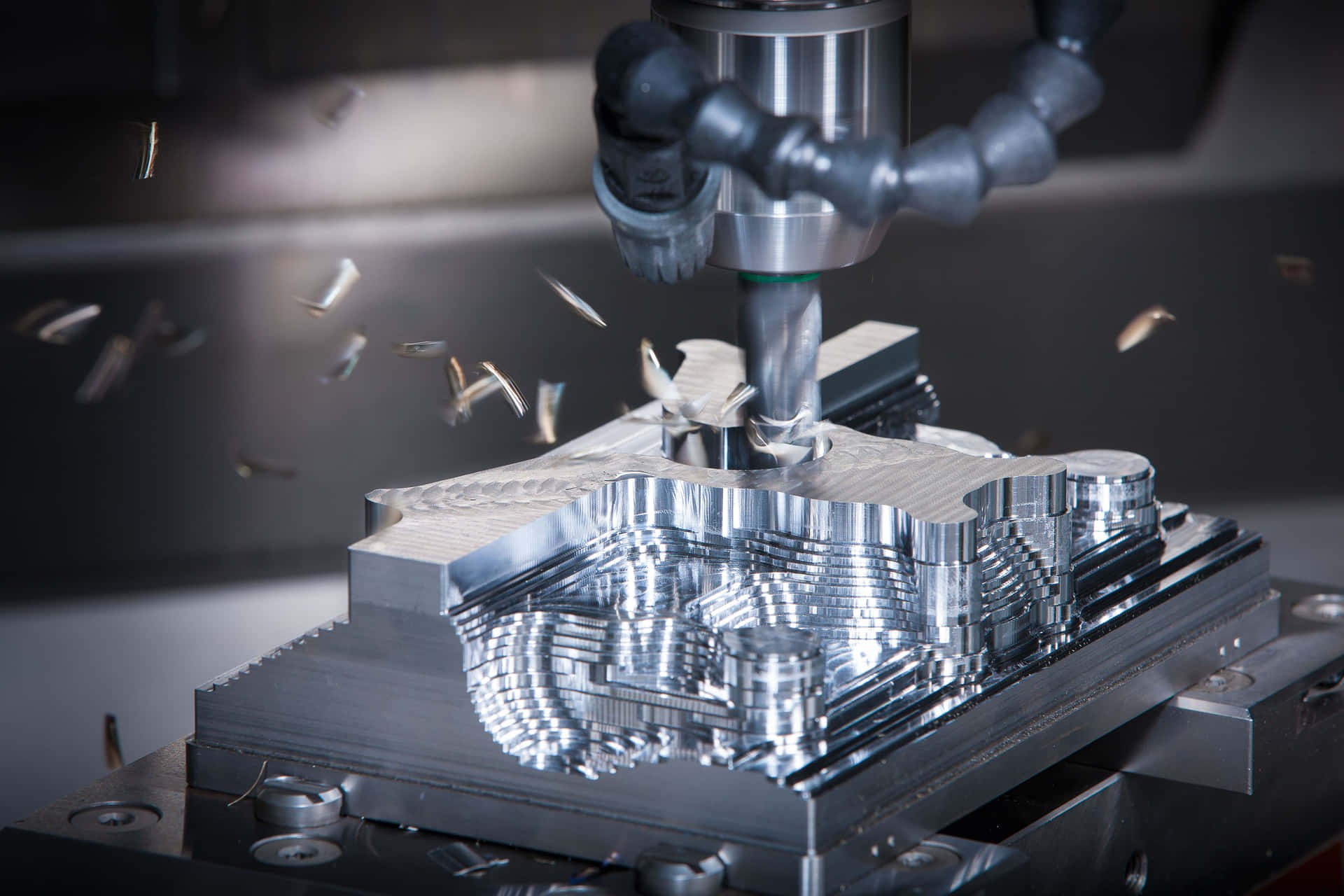
Gantry machining centers are transforming the landscape of industrial manufacturing. These versatile machines have gained prominence due to their ability to handle intricate, complex projects that require precision, speed, and versatility. With their robust design and superior capabilities, gantry machining centers are changing the way industries approach heavy-duty machining tasks. This article explores the advantages and applications of gantry machining centers and why they are a game-changer for complex projects.
What is a Gantry Machining Center?
A gantry machining center is a type of CNC (Computer Numerical Control) machine that utilizes a gantry structure for movement. Unlike traditional vertical or horizontal machining centers, the gantry design allows for greater flexibility and access to large workpieces. The machine consists of a fixed base, columns on either side, and a movable spindle that can travel across the entire structure. This enables efficient handling of large components with high precision, making it ideal for industries that require accurate and large-scale machining.
Key Features of Gantry Machining Centers
Gantry machining centers are equipped with several key features that make them stand out from other machining solutions. The most notable feature is their large working envelope, which allows them to accommodate bulky or oversized parts. These machines can perform various operations such as milling, drilling, and tapping with high precision. Furthermore, their multi-axis capabilities enable intricate and complex machining tasks that are difficult for conventional machines to handle.
The robust construction of gantry machining centers ensures minimal vibration, leading to smoother operations and more accurate results. Their ability to work with various materials, including metals, plastics, and composites, adds to their versatility.
Precision and Accuracy in Complex Projects
One of the primary reasons gantry machining centers are essential for complex projects is their ability to deliver high precision. In industries like aerospace, automotive, and defense, the slightest deviation in measurements can lead to significant defects or failures. Gantry machines are equipped with advanced CNC technology, which ensures that each cut, drill, or tap is executed with utmost accuracy.
These centers are capable of maintaining tight tolerances over extended periods, making them perfect for producing critical components such as turbine blades, engine parts, or structural components. The high level of accuracy achieved with gantry machining centers is unmatched by many other traditional methods.
Versatility in Handling Complex Materials
The versatility of gantry machining centers is another factor that makes them a game-changer for complex projects. These machines are designed to handle a wide range of materials, from hard metals like titanium to softer materials like plastics. Their adaptability makes them highly valuable in industries that work with diverse materials, such as manufacturing, aerospace, and automotive industries.
The ability to switch between different materials without compromising on precision is a significant advantage for manufacturers working on projects that require multiple material types. Whether it is machining metal parts for a car engine or precision components for an aircraft, gantry machining centers excel in delivering consistent results across varied materials.
Efficiency in Large-Scale Production
Gantry machining centers are designed to handle large-scale production with increased efficiency. Traditional machining methods may require multiple setups, tool changes, or different machines to complete a project, resulting in downtime and increased costs. Gantry machining centers streamline this process by offering multi-tasking capabilities in one setup, reducing the need for re-fixturing or transferring parts between different machines.
This increased efficiency not only reduces production time but also lowers the overall cost of manufacturing. With the ability to operate continuously without compromising on quality, gantry machining centers play a pivotal role in mass production environments where time and precision are critical.
Application in Complex Manufacturing Projects
The application of gantry machining centers in complex manufacturing projects is vast and varied. In the aerospace industry, for example, these machines are used to manufacture large, intricate components such as aircraft wings and fuselage parts. The ability to work with oversized parts, coupled with the precision required in aerospace engineering, makes gantry machining centers an ideal choice for these types of projects.
In the automotive sector, these machines are used for producing engine blocks, transmission components, and chassis parts, where accuracy and speed are essential. Similarly, gantry machining centers are used in the manufacturing of large molds for injection molding processes, which are critical in industries like consumer goods and packaging.
Enhancing Productivity with Automation
Another significant advantage of gantry machining centers is their ability to integrate with automation systems. In todayβs manufacturing landscape, automation is key to improving productivity and reducing human error. Gantry machining centers can be paired with robotic arms, automated tool changers, and other advanced systems to create a fully automated production line.
This integration allows manufacturers to achieve continuous production with minimal human intervention, further improving efficiency and reducing operating costs. Automation also ensures that production standards remain consistent throughout, contributing to the overall reliability of the manufacturing process.
Reducing Costs in Complex Projects
While gantry machining centers come with a higher initial investment compared to traditional machines, their long-term cost benefits are significant. The ability to handle multiple tasks in one setup reduces the need for additional machines and labor. Additionally, the increased speed and efficiency result in shorter production times, which directly translates to cost savings.
Moreover, the precision and accuracy of these machines help reduce waste and rework, which can be costly in complex projects. By maintaining tight tolerances and reducing material wastage, gantry machining centers help manufacturers save money over the long term, making them a wise investment for businesses that require high-precision manufacturing.
Future Prospects of Gantry Machining Centers
As technology continues to advance, the capabilities of gantry machining centers are expected to evolve. With the integration of artificial intelligence (AI) and machine learning, these machines could become even more efficient in optimizing machining parameters, predicting maintenance needs, and improving overall performance.
The continuous development of new materials and manufacturing techniques will also drive the demand for gantry machining centers. As industries push for higher precision, faster production, and cost efficiency, gantry machining centers will continue to play a crucial role in shaping the future of manufacturing.
Conclusion
Gantry machining centers have emerged as game-changers for industries handling complex and high-precision projects. Their unmatched versatility, precision, and efficiency make them indispensable tools in industries such as aerospace, automotive, and heavy machinery. With the ability to handle large parts, intricate designs, and diverse materials, gantry machining centers are set to redefine the standards of modern manufacturing.
As these machines continue to evolve with advancements in automation and AI, their impact on complex projects will only grow. Manufacturers who adopt 5 axis machining center will be better equipped to meet the demands of an increasingly competitive and fast-paced industry. Investing in this technology not only enhances productivity but also ensures that businesses remain at the forefront of innovation and quality in their respective fields.
Leave a Reply