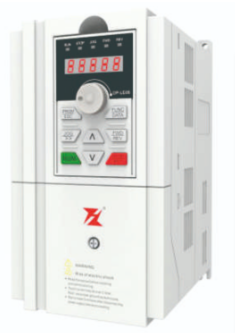
Modern industrial applications depend heavily on Variable Frequency Drives (VFDs) because these components are known by two additional names: inverter drives or variable speed drives. The products allow electric motor speed and torque control through adjustments to both supply frequency and voltage. Increased VFD demand exists because these devices provide both energy-saving advantages together with operational cost reductions and motor performance maximization capabilities. This post explores VFD Inverter manufacturers through an examination of industry innovation alongside market patterns and critical selection criteria for manufacturers.
Importance of VFD Inverter Manufacturers
The production of VFD inverters by manufacturers represents a vital force that drives both industrial automation advancement along energy management refinement. The VFD inverter manufacturers create custom inverters for diverse sectors and system sizes which serve industrial needs across manufacturing factories and transportation as well as HVAC facilities and water treatment facilities. The manufacturers must confirm that their products conform to worldwide safety requirements and total effectiveness and operational reliability standards.
The primary business worth of VFD manufacturers stems from their ability to create solutions that tackle essential problems. Machine-driven energy consumption control through VFD applications supports climate change combat by reducing greenhouse gas emissions. Manufacturers develop precise solutions tailored for demanding operational conditions including mining and oil gas sectors because equipment staleness is essential there.
Technological Advancements by VFD Manufacturers
VFD inverter manufacturers demonstrate constant dedication to technological development as a fundamental business aspect. Manufacturers are integrating smart technologies into VFDs during Industry 4.0 growth to enhance product performance and capacity. Computerized features for IoT integration along with predictive error detection and refined operation controls have become primary standards in today’s VFD systems.
- World-class motor Inverter manufacturers allocate large R&D budgets to build miniature energy-saving VFDs for managing complex motor operations. Control Circuits: These circuits control the operational parameters of the inverter, such as voltage regulation, frequency control, and power factor correction.
- Cooling Systems: Heatsinks and fans are effective thermal management systems that prevent overheating and increase the lifespan of the inverter.
- Enclosures: The enclosures designed by the manufacturers are rugged enough to shield the internal components of the inverter from dust, moisture, and temperature variations.
- The quality and level of accuracy of these parts directly impact the inverter’s performance and reliability.
Technological Developments in Inverter Production
The technological revolution in the sector of inverters has been mighty in recent decades. Especially for higher efficiency, compact designs, and a greater level of performance, technological development in the inverter sector has been tremendous in recent decades. Multilevel inverters, smart inverters, and bi-directional inverters have changed the look of the entire sector.
- Multilevel Inverters: These inverters exhibit higher efficiency and minimal harmonic distortion and thus are more suitable for the industrial sector.
- Smart Inverters: Rich in features of remote monitoring, diagnostics, and grid-support functionalities, these smart inverters are preferred for modern solar and wind power systems.
- Bidirectional Inverters: These will make energy flow in both forward and backward directions, and these inverters may be used at energy storage devices and electric vehicle charging stations.
- Automation and digitalization: In manufacturing processes, including AI and IoT, have made production more efficient, reduced costs, and improved the quality of products.
Inverter Manufacture Challenges
While the inverter manufacturing industry is booming, it has its challenges. These include:
- Cost Pressures: The high cost of raw materials, such as semiconductors and rare earth elements, imposes a challenge to the maintenance of competitive pricing.
- Quality assurance measures in each batch are assured with rigid quality control in the case of mass production.
- Manufacturing inverters requires compliance with regional and international safety, performance, and environmental standards, which is challenging and costly.
- Global pandemics, tension-driven geopolitical reasons, and natural disasters, among many other events, can easily affect the supply chain.
Role of Inverters in Renewable Energy
One of the most important uses of inverters is in renewable energy systems, especially solar and wind power. In solar systems, inverters convert the DC power that photovoltaic (PV) panels generate to AC power to be used for households and the grid. Recent renewable energy inverters possess characteristics such as MPPT and anti-islanding protection on board as standard features.
Future Prospects of Inverter Manufacturing
Folinn Drives Motor Inverter manufacturer demonstrates positive growth prospects because of expanding electric vehicle adoption rates alongside increasing activity in energy storage systems and smart grids. The development of modular inverters with scalable functionality and enhanced efficiency will receive increased focus from manufacturers due to increasing consumer demand for energy independence through decentralized power systems.
Predictive maintenance will benefit from advanced technology integration of AI with machine learning and IoT while leading to improved grid stability and enhanced energy optimization. Growing sustainability demand will lead to eco-friendly inverter creation using recyclable materials while focusing on achieving high energy efficiency levels.
Summary
Inverter manufacturing represents a high-tech industry which maintains critical importance for today’s energy management systems. Through their continuous innovation efforts combined with a universal market analysis of discoverable energy patterns, inverter manufacturers can actively shape forward-thinking sustainable energy systems. Folinn Drives advanced inverters will experience increasing demand in the next decade to support renewable energy transitions and smart technology adoption which will make this industry essential to global power networks.
FAQs
Which fundamental task does an inverter serve?
Through its conversion process, an inverter transforms electricity from direct current to alternating current to run systems and appliances.
Which categories compose the major classification of inverters?
There exist three primary inverter types that perform distinct energy functions standalone inverters and grid-tied inverters plus hybrid ones.
How extensively do inverters find usage across different sectors?
Exact power conversion takes place through inverters for residential and industrial applications and commercial facilities as well as renewable power industries such as wind and solar.
An inverter requires which main components to work?
Inverters require power semiconductors along with control circuits, cooling systems and strong protective enclosures.
What is a smart inverter?
A smart inverter includes sophisticated functions that enable remote device monitoring along with diagnostics tools and automated grid support.
Leave a Reply