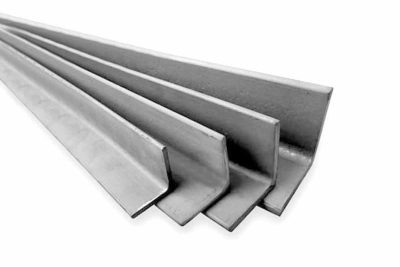
Aluminum alloys are widely used across various industries due to their excellent strength, lightweight nature, and corrosion resistance. Among the many aluminum grades available, 5052 aluminum angle stands out as a top choice for demanding applications. Whether used in construction, marine projects, or industrial settings, this alloy offers unmatched durability and performance.
In this blog, we will explore the properties, applications, benefits, and machining considerations of 5052 aluminum angle to help you understand why it is an ideal material for many industries.
What is 5052 Aluminum Angle?
5052 aluminum angle is a structural component made from 5052 aluminum alloy, which is primarily composed of aluminum (Al) and magnesium (Mg). This alloy is known for its high strength, excellent corrosion resistance, and superior workability. The angle shape is commonly used for support structures, bracing, and reinforcement due to its rigidity and stability.
Key Properties of 5052 Aluminum Angle
The 5052 aluminum alloy possesses a unique combination of mechanical and chemical properties that make it a sought-after material. Here are its key attributes:
1. Corrosion Resistance
-
Exceptional resistance to marine and industrial environments.
-
Resists saltwater, chemicals, and atmospheric corrosion.
2. High Strength-to-Weight Ratio
-
Stronger than many other aluminum alloys, such as 3003 and 6061.
-
Maintains structural integrity under stress while being lightweight.
3. Excellent Weldability
-
Can be easily welded using TIG, MIG, or arc welding.
-
Suitable for projects requiring structural joints.
4. Superior Formability and Workability
-
Can be bent, rolled, and shaped without cracking.
-
Ideal for fabricating complex structures and components.
5. Good Fatigue Strength
-
Performs well in applications with repetitive stress and load cycles.
6. Non-Heat Treatable Alloy
-
Strength is achieved through strain hardening rather than heat treatment.
Common Applications of 5052 Aluminum Angle
Due to its excellent properties, 5052 aluminum angle is used across numerous industries. Here are some of the most common applications:
1. Marine Industry
-
Boat hull reinforcements
-
Dock structures and gangways
-
Offshore platforms
2. Construction and Architecture
-
Structural framing
-
Handrails and guardrails
-
Roofing and awning supports
3. Automotive and Transportation
-
Truck and trailer frames
-
Railcar components
-
Aircraft structural supports
4. Industrial and Manufacturing
-
Machinery and equipment components
-
Conveyor systems
-
Support brackets and shelving
5. Electrical and Energy Sectors
-
Transmission line supports
-
Solar panel mounting frames
-
Wind turbine components
Advantages of Using 5052 Aluminum Angle
Choosing 5052 aluminum angle over other materials provides several benefits:
1. Lightweight Yet Strong
-
Offers high strength without adding unnecessary weight.
-
Easier to transport, install, and handle.
2. Corrosion-Resistant in Harsh Environments
-
Outperforms other alloys in coastal, industrial, and chemical environments.
-
Minimizes maintenance costs due to long-term durability.
3. Highly Versatile for Various Applications
-
Suitable for a wide range of industries and projects.
-
Can be used in both structural and decorative applications.
4. Excellent Workability and Weldability
-
Can be easily fabricated, cut, and shaped.
-
Works well with different welding techniques without compromising strength.
5. Cost-Effective Solution
-
Lower material and maintenance costs compared to steel and other metals.
-
Longer lifespan reduces replacement expenses.
Machining and Fabrication Considerations
Cutting and Machining
-
Use carbide-tipped tools for precision cutting.
-
Avoid overheating to maintain material integrity.
-
Can be sawed, drilled, or milled with ease.
Welding Guidelines
-
Best welded using MIG or TIG processes.
-
Requires proper filler material like 5356 or 5556 aluminum wire for optimal strength.
Surface Finishing Options
-
Can be anodized for enhanced corrosion resistance.
-
Powder coating and painting options available for aesthetic appeal.
Comparing 5052 Aluminum Angle with Other Alloys
5052 vs. 6061 Aluminum Angle
Property | 5052 Aluminum Angle | 6061 Aluminum Angle |
---|---|---|
Strength | Moderate-High | Higher |
Corrosion Resistance | Excellent | Good |
Weldability | Excellent | Fair |
Workability | Superior | Moderate |
Cost | More affordable | Slightly expensive |
Key Takeaway: If corrosion resistance and weldability are priorities, 5052 aluminum angle is the better choice. If higher strength is needed, 6061 aluminum is preferable.
Conclusion
5052 aluminum angle is an outstanding material choice for various industries due to its strength, corrosion resistance, workability, and cost-effectiveness. Whether you need structural support for a marine environment, industrial application, or architectural project, this alloy delivers superior performance.
Leave a Reply