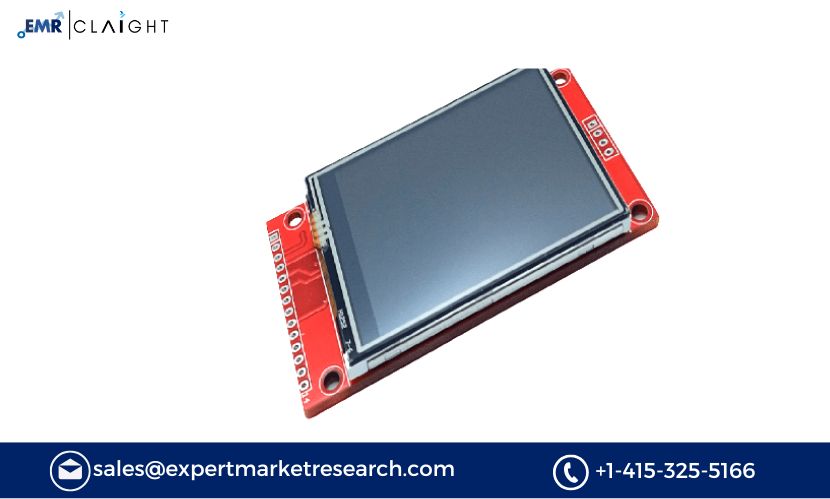
Introduction
The Thin Film Transistor (TFT) Liquid Crystal Display (LCD) technology has revolutionized the display industry, offering high-resolution, energy-efficient, and thin screens for a variety of applications. From smartphones and televisions to computer monitors and automotive displays, TFT LCDs have become the go-to technology for modern-day screens. As the demand for high-quality, energy-efficient displays continues to grow, establishing a TFT LCD Manufacturing Plant offers immense business opportunities. A TFT LCD Manufacturing Plant Project Report is a crucial document for entrepreneurs and investors seeking to set up a manufacturing facility for this rapidly growing market. This report serves as a blueprint, detailing the plant setup, machinery, financial projections, market potential, and operational strategies necessary to successfully enter the TFT LCD manufacturing industry.
Overview
TFT LCD technology involves the use of a thin-film transistor to control individual pixels within a liquid crystal display. Unlike traditional LCDs, which use passive matrices, TFT LCDs offer superior image clarity, faster refresh rates, and enhanced color accuracy, thanks to active matrix control. These advantages make TFT LCDs ideal for high-definition displays in consumer electronics, automotive dashboards, medical equipment, and digital signage.
The global demand for TFT LCD displays is driven by the growing adoption of smart devices, demand for high-quality televisions, and increasing use in automotive and industrial applications. This surge in demand has prompted the need for more TFT LCD manufacturing plants capable of producing displays in large volumes while maintaining high quality.
Key Components
A comprehensive TFT LCD Manufacturing Plant Project Report must cover all facets of setting up and operating a TFT LCD production facility. The key components of the report include market analysis, manufacturing process, infrastructure requirements, financial planning, and human resources management. Let’s take a closer look at each of these components.
Get a Free Sample Report with Table of Contents@
Market Research and Feasibility Study
The first step in setting up a TFT LCD manufacturing plant is conducting thorough market research and a feasibility study to assess the demand and competition. This section of the project report includes:
-
Market Demand: Evaluating the growing demand for TFT LCDs across various industries. This involves understanding the increasing need for displays in consumer electronics, automotive, healthcare, and industrial applications.
-
Competitive Analysis: Analyzing competitors within the TFT LCD market, including key manufacturers, their product offerings, pricing strategies, and market share.
-
Industry Trends: Identifying emerging trends such as the shift towards OLED displays, curved screens, and flexible displays. Understanding these trends helps in designing products that meet future market needs.
Product Specification and Manufacturing Process
The manufacturing of TFT LCDs involves a highly complex and precise process, requiring specialized machinery and materials. The TFT LCD Manufacturing Plant Project Report should detail the following aspects:
-
Product Specifications: Outlining the various types of TFT LCD displays to be produced, such as small-sized displays (for mobile devices), medium-sized displays (for monitors), and large-sized displays (for televisions).
-
Manufacturing Process: The TFT LCD production process is a multi-step procedure that involves:
- Substrate Preparation: A glass or plastic substrate is prepared as the base for the TFT panel.
- Deposition of Thin Films: Thin films of materials such as silicon are deposited onto the substrate using processes like sputtering or chemical vapor deposition (CVD).
- Etching and Patterning: The deposited films are etched and patterned to form the thin-film transistors that control each pixel.
- Pixel Matrix Formation: The TFTs are arranged in a matrix configuration to create the pixel grid for the display.
- Assembly and Bonding: The panel is assembled by bonding the TFT layer with a liquid crystal layer and a polarizing film.
- Final Testing and Inspection: The display is thoroughly tested for defects, color accuracy, and performance before being packaged.
-
Raw Materials: Key raw materials in TFT LCD production include high-quality glass, liquid crystal compounds, conductive films, and polarizers. These materials need to meet strict quality standards to ensure the performance and durability of the final product.
Plant Location and Infrastructure
Selecting the right location for the TFT LCD manufacturing plant is essential for operational success. The project report should consider:
-
Location Criteria: Factors such as proximity to suppliers of raw materials, transportation infrastructure, access to skilled labor, and regulatory environment should influence the location decision. Urban or industrial zones with reliable utilities (water, electricity) and waste management systems are typically preferred.
-
Plant Design and Layout: The manufacturing facility must be designed to accommodate various stages of production, including cleanroom areas for sensitive processes, storage areas for raw materials and finished products, and assembly lines. The layout should be optimized to ensure efficient workflow and minimize contamination risks.
-
Cleanroom Facilities: Due to the delicate nature of TFT LCD production, cleanroom environments are essential. These rooms maintain low levels of airborne particles, preventing dust and contaminants from affecting the display’s performance.
Machinery and Equipment
The TFT LCD manufacturing process requires a wide range of specialized machinery. The TFT LCD Manufacturing Plant Project Report should include:
- List of Machinery: The essential machinery includes:
- Glass Cutting and Grinding Machines: Used to prepare substrates.
- Deposition Equipment: For depositing thin films onto substrates.
- Etching and Lithography Machines: Used for patterning and etching the thin films to create transistors.
- Liquid Crystal Filling Machines: For filling the display panels with liquid crystal material.
- Testing and Inspection Equipment: To test the quality of the final products, including visual inspection systems, color calibration systems, and electrical testing tools.
- Machine Specifications: The project report should outline the specific types of equipment required, such as automated pick-and-place machines, screen printing equipment, and bonding machines, along with their technical specifications and capacity.
Quality Control and Compliance
Quality control is crucial in the TFT LCD industry to ensure that displays meet international standards. The project report should include:
-
Quality Assurance Procedures: Detailed protocols for checking the quality of raw materials, in-process production, and finished products. These should cover aspects such as resolution, color accuracy, contrast ratio, and overall display performance.
-
Regulatory Compliance: TFT LCD manufacturing is subject to strict industry standards and certifications, including ISO 9001 (for quality management systems) and ISO 14001 (for environmental management). Compliance with local and international regulations ensures that the plant operates within legal frameworks and meets product safety standards.
-
Testing and Validation: The plant should have a dedicated testing and validation department to check for issues such as dead pixels, color imbalances, and electrical failures. Reliability testing and burn-in testing are standard practices in the industry.
Financial Planning and Cost Analysis
A well-detailed financial plan is essential for assessing the profitability and feasibility of the TFT LCD manufacturing plant. The TFT LCD Manufacturing Plant Project Report should include:
-
Capital Investment: A detailed breakdown of the initial capital required for purchasing land, machinery, infrastructure, and raw materials. It should also account for installation costs, research and development, and other setup expenses.
-
Operating Costs: Ongoing operational costs include raw material procurement, utility expenses, labor wages, maintenance of machinery, and other day-to-day expenses.
-
Revenue Projections: Based on market demand and production capacity, the project report should include sales forecasts and revenue projections for the first few years of operation.
-
Break-even Analysis: The report should calculate the break-even point, i.e., the time it will take to recover the initial investment based on expected sales volume and price per unit.
-
Profitability and ROI: A detailed return on investment (ROI) analysis, including the expected profit margins and the time frame for achieving profitability.
Human Resource Requirements
Running a TFT LCD manufacturing plant requires a skilled workforce. The project report should cover:
-
Staffing Needs: Identifying key personnel needed in areas such as production, quality control, research and development, sales and marketing, and administration.
-
Training and Development: Ensuring that workers are adequately trained in operating specialized equipment, adhering to safety procedures, and maintaining quality standards.
-
Employee Welfare: Addressing the welfare of employees through competitive wages, benefits, safety measures, and career development opportunities.
Marketing and Sales Strategy
To achieve commercial success, the manufacturing plant must have a solid marketing and sales strategy. The TFT LCD Manufacturing Plant Project Report should include:
-
Target Market: Identifying key customers, including electronics manufacturers, automotive companies, and other businesses requiring TFT LCD displays.
-
Sales Channels: Developing a network of distributors, OEMs (Original Equipment Manufacturers), and direct sales strategies.
-
Branding and Positioning: Establishing a brand identity for high-quality, reliable TFT LCDs. The plant should focus on competitive pricing, product differentiation, and customer service to gain market share.
Media Contact
Company Name: Claight Corporation
Contact Person: Lewis Fernandas, Corporate Sales Specialist — U.S.A.
Email: sales@expertmarketresearch.com
Toll Free Number: +1–415–325–5166 | +44–702–402–5790
Address: 30 North Gould Street, Sheridan, WY 82801, USA
Website: www.expertmarketresearch.com
Aus Site: https://www.expertmarketresearch.com.au
Leave a Reply